Why is Lean Six Sigma still a significant business model in 2022?
Using Lean Tools to Solve Problems Effectively
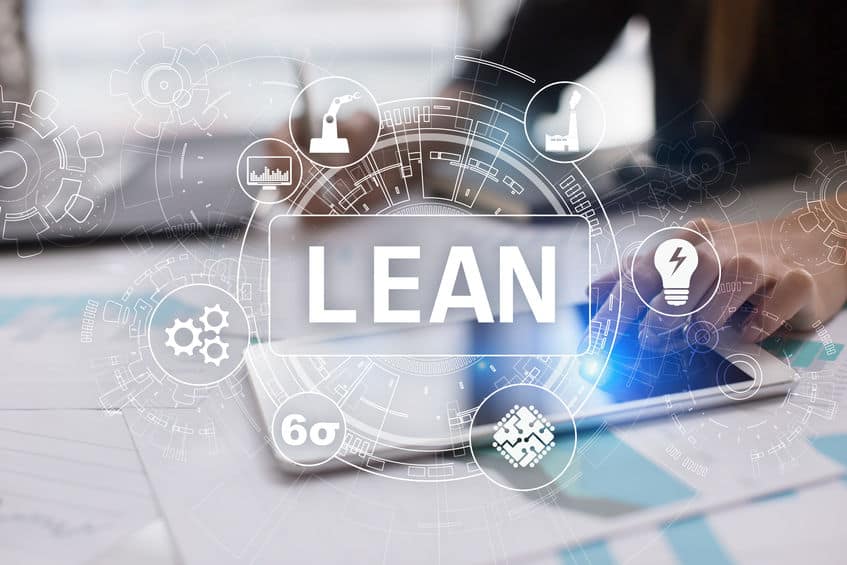
The combination of Lean tools and strategies used to get to the bottom of a problem or issue in quality management is fundamentally part of Root Cause Analysis (RCA). Although some people like to solve problems in an ad hoc manner, RCA’s tools make the process more systematic and rigorous. This has been shown to provide outstanding outcomes.
Some of the tools help you to explore beyond the obvious to find the root reason. Others enable you to picture the situation in order to examine it from a new angle. And each tool is meant to assist you in identifying the true, hidden issue, which will prevent the problem or issue from recurring once it has been resolved.
This saves the team a significant amount of time. Patchwork is nothing more than constantly working on surface issues. If the root cause is not addressed, the problem will return, potentially getting worse with each occurrence. It also keeps the team from concentrating on the wrong problem or one that doesn’t need to be solved at all.
When it comes to RCA, clubs have a variety of options. The most prevalent ones are listed below.
Lean Tools: Fishbone Diagram
The fishbone graphic is utilized when the problem at hand is complicated. It enables the team to divide potential causes into homogenous and sub-groups. It’s especially useful when the fundamental cause is obscured by a variety of superficial issues. The cause-and-effect diagram is another name for the diagram.
Lean Tools: 5 Why’s
The 5 Whys engages you in the role of a detective attempting to solve a mystery. It’s also not difficult because all you have to do is ask the question “Why?” ” five times – as a guideline, not a rigid rule – until the root problem is discovered. It works well on basic topics, thus it might not be the ideal choice if the quantitative analysis is required.
Pareto Chart
The effects noticed 80% of the time are due to 20% of the time causes. The essential premise of the Pareto Chart is this. This visualization tool gives a glimpse of typical faults so they may be quickly identified. It lists their causes in descending order to assist you to deal with them in the order of importance and urgency.
Failure Mode and Effect Analysis (FMEA)
When a system experiences a specific failure, the FMEA is the finest instrument for shedding light on it. The Failure Mode feature of the application allows you to brainstorm probable causes of system failure. These are the many types of failures. The impacts of each of the failure types discovered in the preceding stage are investigated further in Effects Analysis.
Conclusion
One of the numerous ways organizations accomplish Six Sigma is to take Root Cause Analysis seriously. Because each problem is unique to the company, there is no one-size-fits-all approach to RCA. While additional tools may be used to perform RCA, these are the ones that successful companies employ on a regular basis. Each one has been proven time and time again to be helpful in permanently resolving difficulties and issues.
Here at CourseMonster, we know how hard it may be to find the right time and funds for training. We provide effective training programs that enable you to select the training option that best meets the demands of your company.
For more information, please get in touch with one of our course advisers today or contact us at training@coursemonster.com