There’s more at stake here than a misunderstanding and a headache. Misunderstandings regarding Six...
Lean Six Sigma: Project Management with 6 Sigma Certification
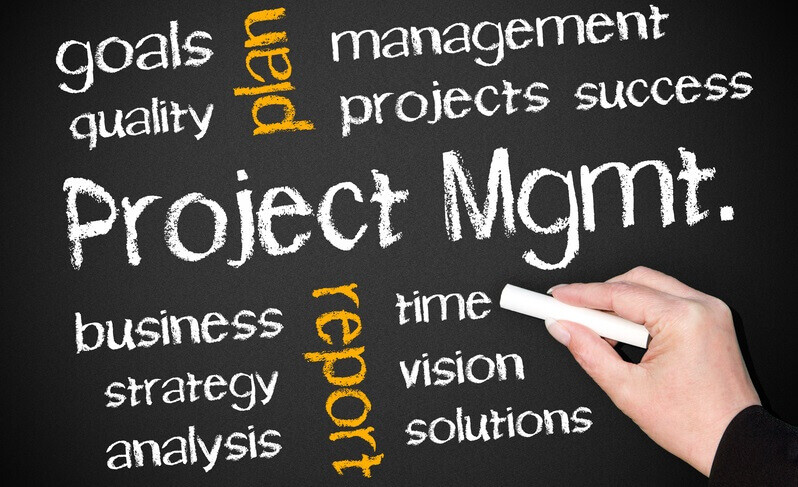
According to the Worldwide Project Management Survey Pulse, 12% of global firms were classified as under-performers in 2017. The list featured businesses from a wide range of industries, including the government, information technology, 6 sigma certification and financial services.
Project management was summarized in the survey. It demonstrated that 60 percent of the organization’s initiatives were completed on schedule and on budget. The absence of specified and measurable milestones and targets to monitor progress was also noted in the other initiatives.
Any project manager’s principal goal is to enhance productivity. They must be aware of the wide range of technologies, methods, and processes that might affect project delivery best practices.
Although current technology and procedures have shown a favorable upward trend in project delivery, there is still a growth gap that may be addressed by incorporating Lean Six Sigma into company operations.
Throughout the framework, the goal is to follow a repeatable process to achieve a good end and get a greater understanding of how integration may be accomplished.
What is Project Management?
Project management, according to PMI, is “the application of knowledge, skills, tools, and procedures to activities to achieve project requirements.”
Every project, from start to completion, needs a plan that describes how things will get started, how they will be created, and how they will be finished.
What is Lean Six Sigma?
Lean Six Sigma is a performance improvement strategy that focuses on a collaborative team effort to eliminate waste and reduce variance.
Minimizing variability, waste, and cycle time while increasing job uniformity and flow, improves customer satisfaction and outcomes.
The DMAIC (Define, Measure, Analyze, Improve, and Control) approach is often used to execute projects while using Lean Six Sigma.
Want to know more about Lean Six Sigma? Visit our course now.
6 Sigma Certification: DMAIC Improvement Process
The DMAIC model refers to problem-solving procedures that are used to continuously enhance an existing process. The technique is targeted at enhancing product/service quality.
DMAIC’s 5 phases are:
1. Define – Project teams create a high-level process map to define the demands of customers at this phase.
Tools used:
- Project charter
- Tree diagram
- Value stream map
- Relationship map
- Stakeholder analysis
- VOC (Voice of Customer)
2. Measures – The data-gathering plan is the focus of this stage. You develop and execute data that indicates how the process is doing, assisting in the delivery of variance, in this process.
Tools used:
- Project charter
- Data collection plan
- Operational definitions
- Check sheet
3. Analyze – Teams can calculate the financial rewards of fixing the challenge at this point.
Tools used:
- Value stream map
- Fishbone diagram
- Value-added flow analysis
- Gantt charts
- Pareto charts
- Root cause analysis
- 5 why’s
4. Improve – This stage relies on the team’s inventiveness to solve the process challenge.
Tools used:
- Value stream map
- Brainstorming sessions
- Benchmarking
- Weighted criteria matrix
- Impact/Effort matrix
- Pilot checklist
- Implementation plan
5. Control – This phase allows the team to report the new solution they’ve developed so that it can be passed on to the process owners.
Tools used:
- Control plan (or a control chart)
- Monitoring and response plan
- Innovation transfer opportunities
- Gallery walks
- Documentation
Lean Six Sigma Integration in Project with 6 Sigma Certification
DMAIC, a Six Sigma technique, provides a planned and disciplined approach to tackling business challenges. It pinpoints the source of faults in the business process, ensuring high quality throughout the project lifetime. Cross-functional teams are frequently used in Lean Six Sigma projects. The technique, on the other hand, does not explicitly handle project management.
Throughout the project management process, a variety of Lean Six Sigma approaches are applied. Project managers employ work breakdown analysis, schedule development, risk analysis, scope definition, status reporting, and cost budgeting to plan, execute, control, and conclude projects.
These approaches enable project managers to make smart and informed decisions as they progress from phase to phase throughout the project lifecycle. Project management and Six Sigma technologies may be used to plan, act, do, and check a process improvement project throughout the lifespan. In addition, approaches and procedures can be combined to improve the process.
The Advantages of Lean in Projects with 6 Sigma Certification
Decision Making – Every defect/error has a data-based evidence approach in every Six Sigma technique. This procedure is more accurate than any other way.
Time-Saving – The advice of a Lean Six Sigma specialist at the start of each project defines the scope and deliverables precisely, as well as the efficient use of resources.
Cost Saving – Cost savings are a direct result of implementing Lean Six Sigma because the methodology’s primary goal is to minimize mistakes and defects.
Increase in Productivity with 6 Sigma Certification – Because every member of the team is committed to the Lean Six Sigma methodology, productivity doubles, freeing up resources for other modules.
Conclusion
To acquire a more complete insight into the total process, the Lean Six Sigma methodology may be combined with project management procedures. Lean Six Sigma improves the capacity of businesses that exclusively utilize project management to make decisions based on evidence-based data and aspects that are important to quality and end-users especially with 6 Sigma Certification.
Here at CourseMonster, we know how hard it may be to find the right time and funds for training. We provide effective training programs that enable you to select the training option that best meets the demands of your company.
For more information, please get in touch with one of our course advisers today or contact us at training@coursemonster.com