When you choose to continue to Lean Six Sigma (LSS) Green Belt Training, you’re indicating that...
Lean Six Sigma Green Belt Certification: Enhancing IT Processes
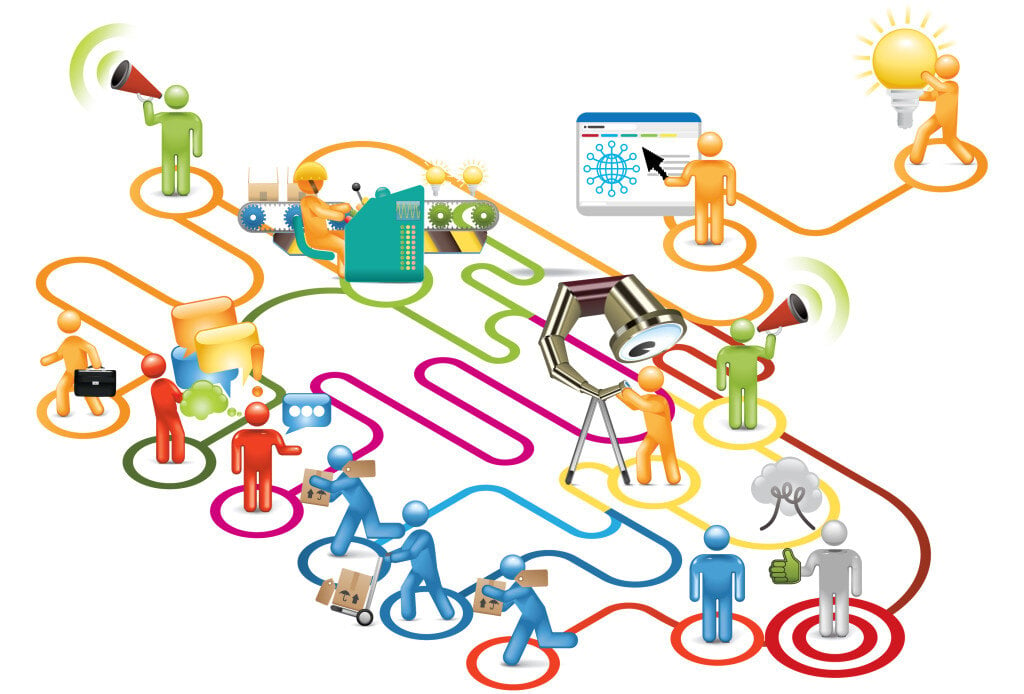
Achieving the Lean Six Sigma Green Belt certification marks a crucial milestone in mastering the Lean Six Sigma methodology and assuming leadership in driving improvement initiatives within an organization. Expanding upon the knowledge and competencies acquired during LSS Yellow Belt training, individuals holding the LSS Green Belt certification play a pivotal role in identifying critical improvement opportunities and taking charge of implementing the requisite transformations.
Why do I need a Lean Six Sigma Green Belt?
As an individual holding the LSS Green Belt certification, you will be presented with the opportunity to lead and execute small-scale improvement projects that have the potential to bring a profound sense of accomplishment. There are few things as empowering as knowing that your efforts have made a genuine impact on your company’s productivity and financial performance.
While LSS Yellow Belts contribute support during the initial stages of an improvement project, such as gathering data and creating process maps, LSS Green Belts are actively involved throughout the entire process. Under the guidance and supervision of an LSS Black Belt or Master Black Belt, Green Belts are the driving force behind implementing the identified improvements.
Professionals with LSS Green Belt certification typically allocate between 25% and 50% of their working hours to LSS projects. They are widely recognized as experts in LSS methodology and serve as catalysts for promoting quality within their organizations.
What jobs require Lean Six Sigma Green Belt Certification?
Professionals who possess LSS Green Belt certification have access to a wide range of job opportunities, which include but are not limited to the following:
Continuous Improvement Manager – Continuous improvement managers are frequently found in the manufacturing sector, where their primary responsibility is to enhance production efficiency by assessing and evaluating organizational procedures. These professionals play a crucial role in driving the continual improvement of essential processes and systems. They are tasked with identifying new metrics to gauge efficiency, as well as implementing programs that yield long-term business advantages.
Quality Engineer – In the role of a quality engineer, your primary responsibility will be to ensure that your organization’s products or services meet the specified customer standards. This entails collaborating closely with diverse stakeholders, including customers, design teams, suppliers, and manufacturing teams, to identify any potential issues that could affect the overall quality of the final product. Quality engineers are typically accountable for generating relevant documentation related to quality standards and designing and executing quality tests.
Quality Manager – The role of a quality manager is occasionally mistaken for that of a quality engineer. However, there are distinct differences between the two. While a quality engineer primarily focuses on bottom-up quality improvement, a quality manager assumes comprehensive ownership of quality within an organization. Key responsibilities of a quality manager encompass understanding customer requirements to establish efficient quality control procedures, formulating and evaluating product and process specifications, and establishing and overseeing compliance with raw material prerequisites from suppliers.
Process Analyst – Process analysts, also referred to as improvement analysts, play a crucial role in assisting organizations in identifying areas for process and performance enhancement. They accomplish this by conducting interviews with internal staff and conducting on-site observations to assess the utilization of suitable equipment, personnel, and methods. In addition, process analysts are responsible for staying updated on industry trends to identify any technological advancements that could potentially result in even greater process efficiencies.
What salary can you earn as an Lean Six Sigma Green Belt?
As per Salary.com, the average salary for individuals holding LSS Green Belt certification in the United States is $101,500 (data as of July 30, 2019). The salary range typically falls between $83,100 and $109,300 and can be influenced by various factors, including additional skills and certifications, level of education, years of experience in the profession, and the specific industry.
On the other hand, Indeed.com estimates the average salary of a certified Green Belt to be around $95,261. Additionally, ASQ’s Quality Progress Salary Survey indicates that Green Belts earn over $10,000 more than Yellow Belts.
What is the difference between LSS Green Belt and Black Belt?
Green Belts typically hold less of a leadership role compared to Black Belts, which is why the latter often command higher salaries. Generally, project teams consist of Green and Yellow Belt professionals who work under the guidance of a certified Black Belt to implement improvements.
While Green Belts possess a solid understanding of LSS methodologies, their knowledge may not be as advanced as that of Black Belts. However, they still have the necessary skills to solve quality issues and conduct analysis using relevant tools. On the other hand, Black Belts have a comprehensive understanding of LSS, which they can impart to both Green and Yellow Belts. They also possess the capability to lead successful improvement projects.
To begin training as a Green Belt, professionals usually require a minimum of three years of work experience. Conversely, Black Belts must already hold certification at the Green Belt level and have at least three years of experience in a specific area of LSS practice.
Want to know more about Lean Six Sigma? Visit our courses now.
Here at CourseMonster, we know how hard it may be to find the right time and funds for training. We provide effective training programs that enable you to select the training option that best meets the demands of your company.
For more information, please get in touch with one of our course advisers today or contact us at training@coursemonster.com