The zero-trust security model has proven to be one of the most successful cybersecurity strategies...
Is Zero Trust the Solution for Cyber Security in Smart Factories?
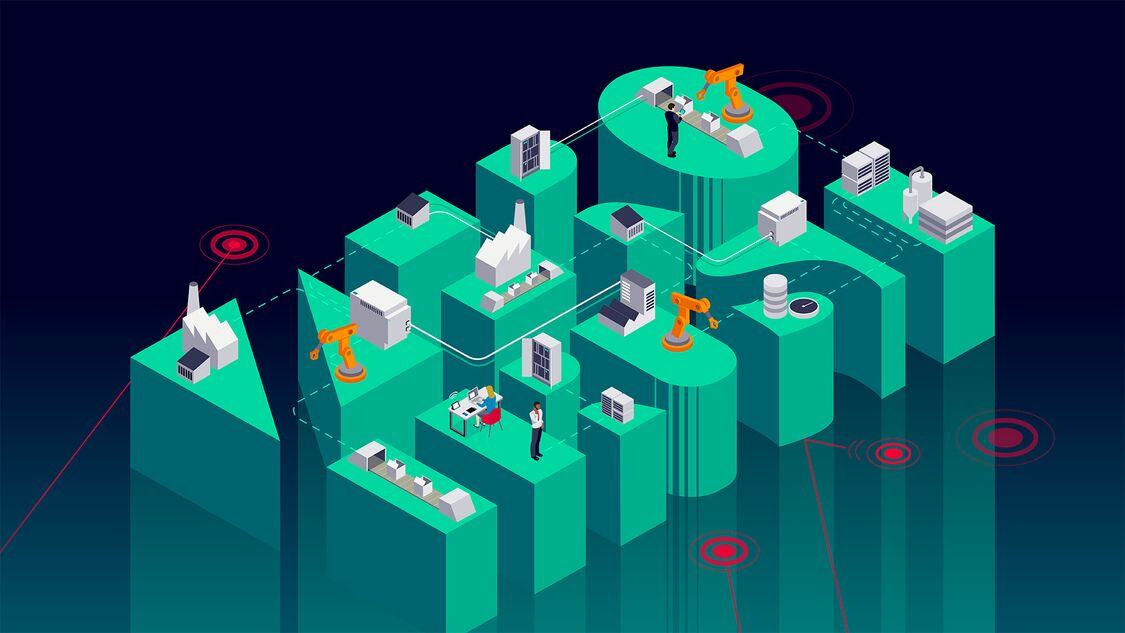
Manufacturing performance and productivity increase as a result of smart factories using zero trust. Key Performance Indicators (KPIs) like labor productivity, factory production, and utilization can increase by 12%. More comprehensive benefits may go beyond manufacturing-specific KPIs and include the development of a digital supply network, which is a highly connected supply chain. However, this increases the risk of cyberspace. In this post, they analyze both issues and possible solutions.
Using Zero Trust in Smart factories and new commercial models
Industry 4.0 technologies are used in a smart factory, a physical and virtual space, to improve operational efficiency throughout the digital organization. They are essential parts of a digital supply chain and are placed in a hyperconnected ecosystem that enables quick access to systems and the transfer of technical, performance, operational, and commercial data both inside and outside the organization. This enhances safety, productivity, and visibility. To provide a real-time perspective of the product lifecycle, hyperconnectivity creates a digital thread that runs through the key components of the organization.
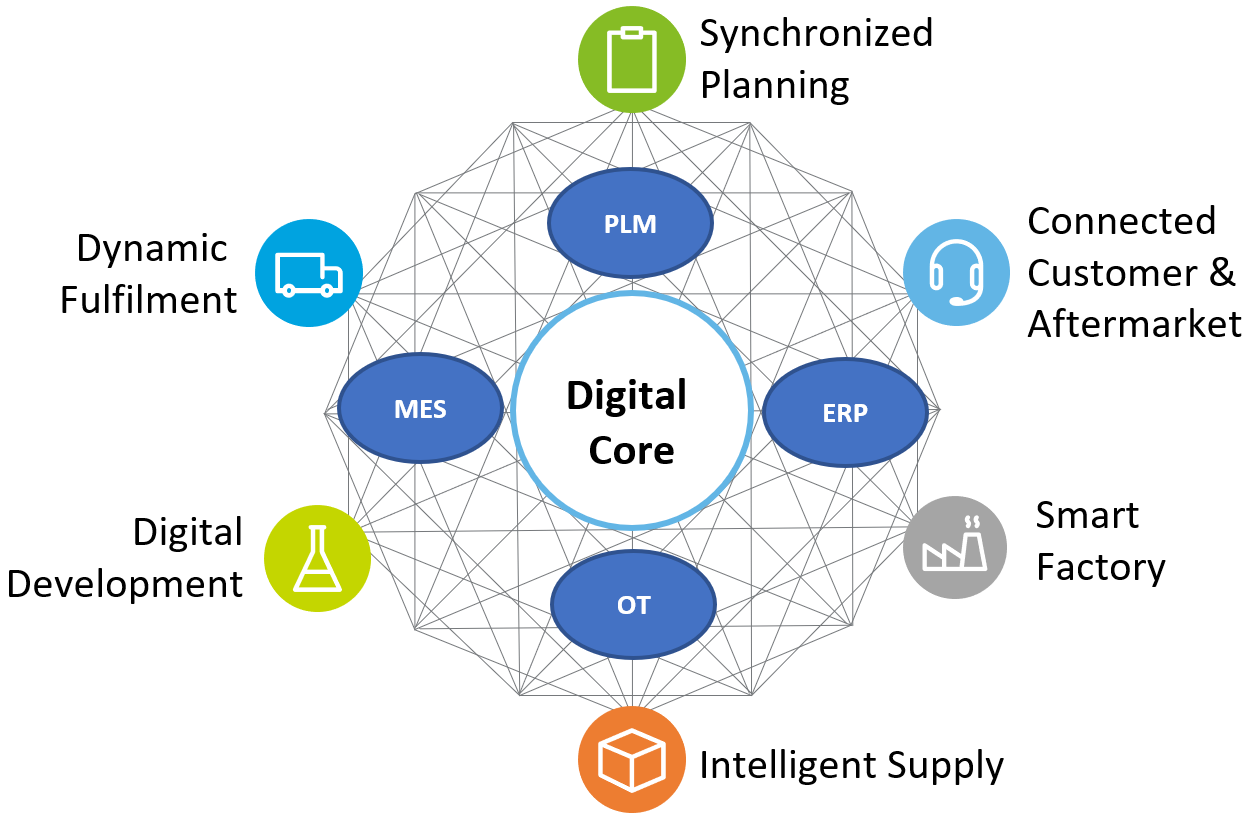
Then, the smart factory joins the larger digital supply chain that many businesses are utilizing to create Anything-as-a-Service (XaaS) business models to provide the manufacturer with utilization annuity revenue and lower capital costs for the consumer. Real-time product monitoring, product usage, and quick improvements and upgrades make this possible, creating organizations that are data-rich and intelligence-driven.
Implications of hyperconnectivity in Zero Trust
Since many organizations are transitioning to a hyperconnected business without understanding the real risk to themselves and others, it is important to better understand the cyber risks to take advantage of the business advantages and opportunities presented by these technological developments. Given that manufacturing surpassed financial services in 2021 as the business most likely to be targeted by cyberattacks, this is very important.
A cyber incident at the manufacturing is not an isolated occurrence since hyperconnectivity increases the blast radius of an assault. One area of the organization may be exposed, which would affect all of its business partners. Most incidents to which they responded either had a direct or indirect effect on other supply chain organizations. For businesses with strict quality assurance requirements, this could be harmful because it could make their items unsellable.
What is the approach?
There is no “silver bullet,” but developing incident response capabilities and a “zero-trust” security approach are good places to start.
The negative effects of hyperconnectivity can be reduced, and the amount of recovery time needed, by controlling the blast radius and having strong prevention, detection, and reaction capabilities. Limiting disruptions and restoring operations to the levels necessary for a viable business also depends on having quick recovery capabilities. The practice and execution of these four core competencies should be quantified, with specific costs and deadlines.
Smart factories and digital supply networks require a strategy that dismisses outdated concepts of “business-disabling” cyber and moves them closer to concepts consistent with the digital supply chain. The zero-trust security approach, whose guiding premise is “never trust, always verify,” may have a lot of promise, according to Deloitte. The zero-trust model abandons the usual “perimeter-based” concept that limits the freedom of the company in favor of one where trust is built between specific resources and customers.
Therefore, the zero-trust approach is ideally positioned to offer agility and scalability while lowering the costs and complexity of cyber management. This is important when moving to a model without borders where the limitations of traditional technologies no longer apply. Data may connect with the business through the digital thread freely thanks to this. Creating a smart factory and its digital supply chain requires achieving free data movement.
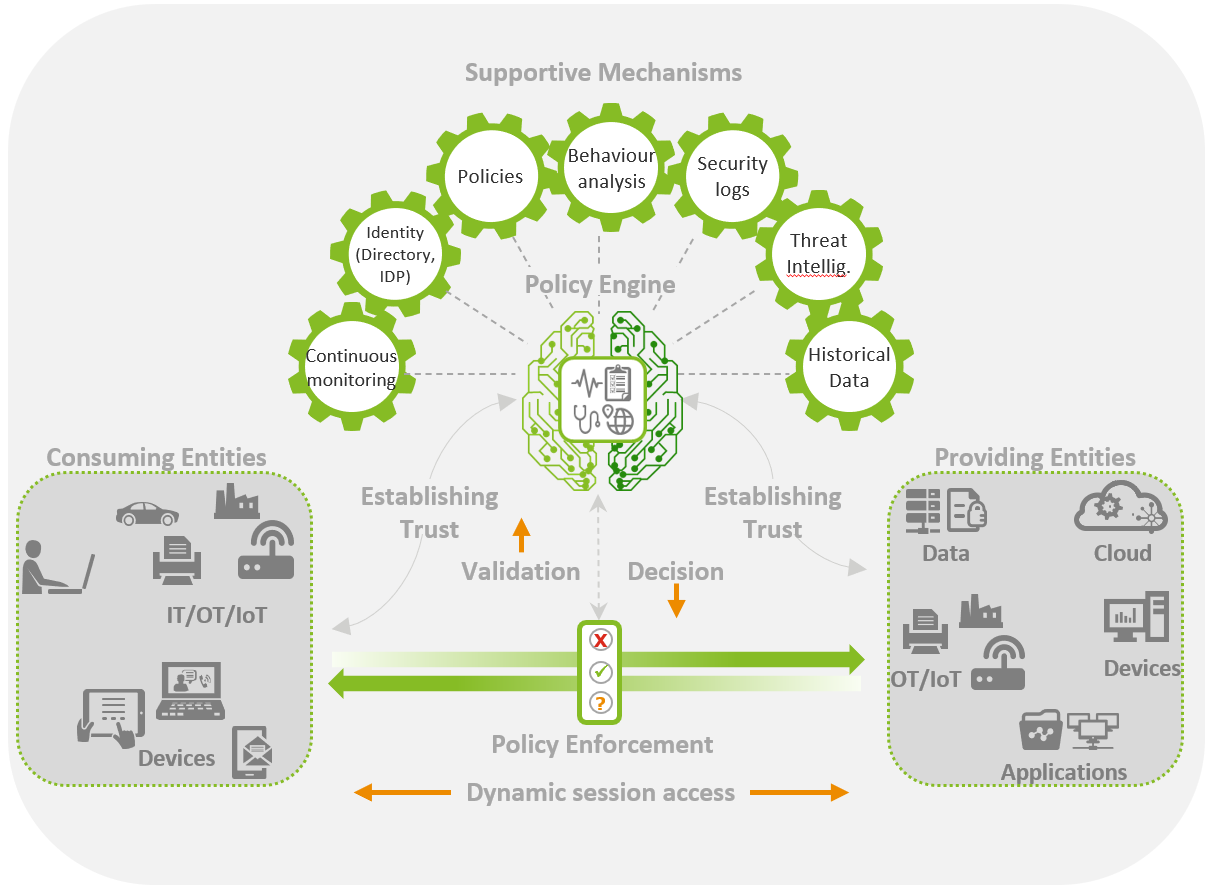
Conclusion
Initiatives to create smart factories are spreading. As you embark on your journey toward a smart factory and a digital supply network, be careful to manage risk from the outset, including security in the design, and do all of this in a way that makes it possible. The objective is to recognize supply chain vulnerabilities and put mitigation measures in place.
Here at CourseMonster, we know how hard it may be to find the right time and funds for training. We provide effective training programs that enable you to select the training option that best meets the demands of your company.
For more information, please get in touch with one of our course advisers today or contact us at training@coursemonster.com